High Quality DTF Film Roll
from China
Wellye is a leading manufacturer and supplier of DTF Film Roll in China. Wellye has been focusing on digital printing consumables for many years, specializing in the manufacture and sale of DTF FILM, PET Film, thermal sublimation paper, DTF transfer paper, thermal transfer paper and other digital consumables. Our products are exported to many overseas countries and are well received by customers all over the world.
Professional DTF Film Roll Manufacturer

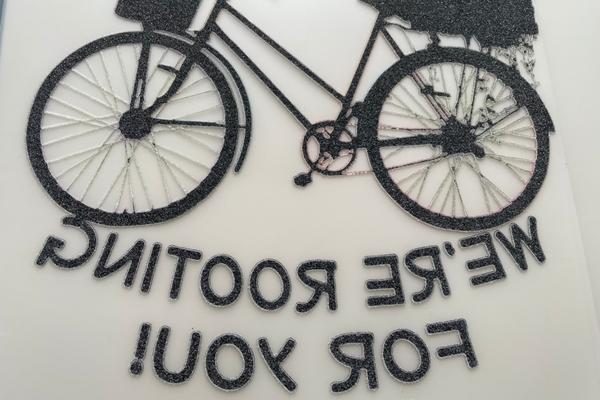
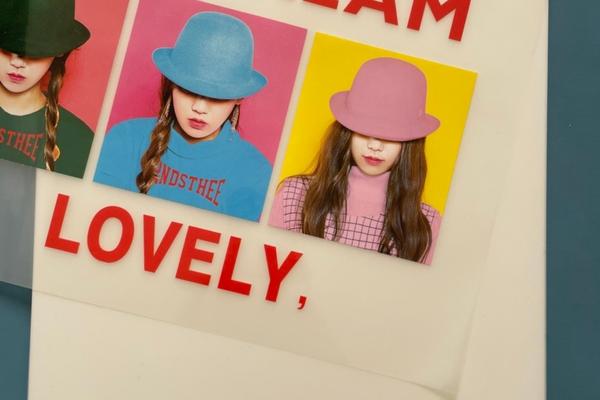
Product We Provide
Types of DTF Supplies We Provide
DTF PET Transfer Film Roll
DTF water-based white ink printing film is a new type of digital heat transfer printing film. Our DTF printing films are easy to peel off and have bright colors. Has good ink absorption and breathability. Compared with weak solvent printing, it has better environmental protection.
Advantages of DTF PET Transfer Film Roll:
-
Compatible hot or cold peel off
-
Strong ink absorption
-
No holes, bubbles
-
Easy to peel, easy to shake powder
-
Vivid and colourgul
-
Shelf life 2 years
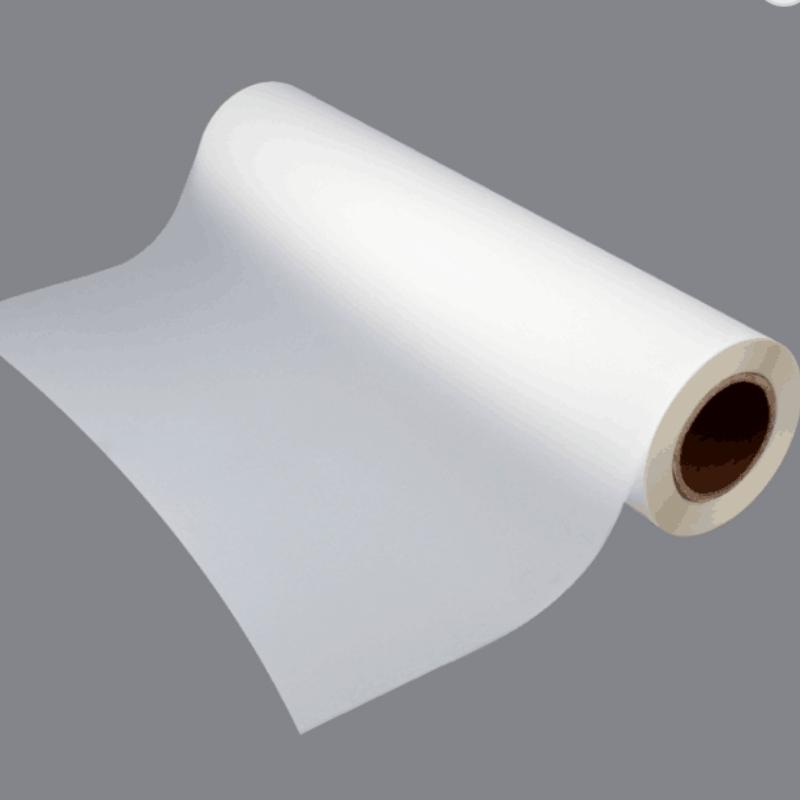
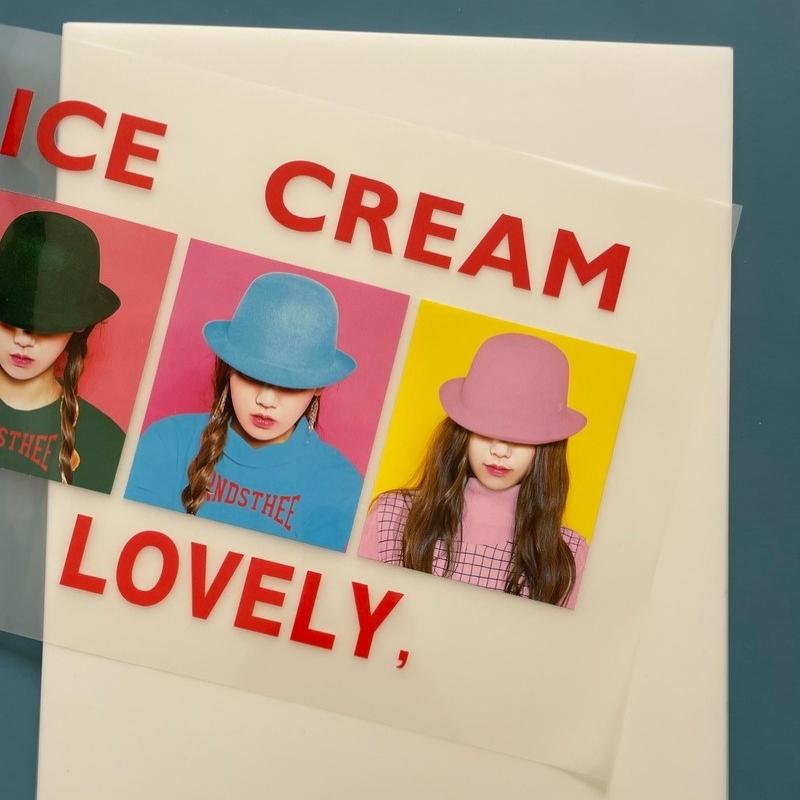
DTF PET Transfer Film Sheet
DTF water-based white ink printing film is a new type of digital heat transfer printing film. Our DTF printing films are easy to peel off and have bright colors. Has good ink absorption and breathability. Compared with weak solvent printing, it has better environmental protection.
Advantages of DTF PET Transfer Film Sheet:
-
Compatible hot or cold peel off
-
Strong ink absorption
-
No holes, bubbles
-
Easy to peel, easy to shake powder
-
Vivid and colourgul
-
Shelf life 2 year
DTF Ink
DTF Printing film ink heat transfer printing film ink is a new type of water-based paint ink, which has good ink stability, good fluency, and reduces the maintenance cost of the bumper. CMYK color ultra-high density, brilliant and saturated color, strong white ink covering power, high whiteness. White color inks have good compatibility and do not penetrate each other.
Advantages of DTF PET Ink:
-
Good fluency
-
High precision
-
Saturated and vivid colors
-
Good color fastness, rubbing resistance, not easy to fade
-
Stretching and not easy to crack
-
Good machine protection
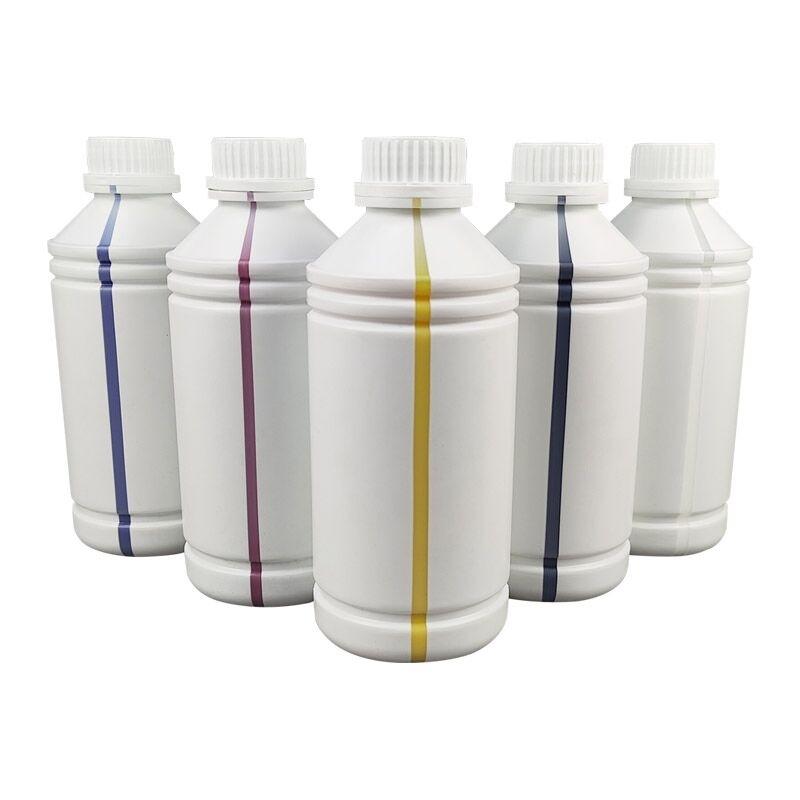
Why Choose Us
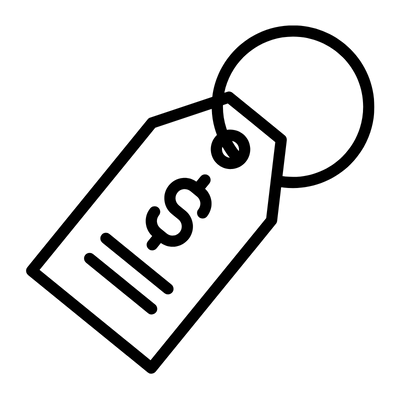
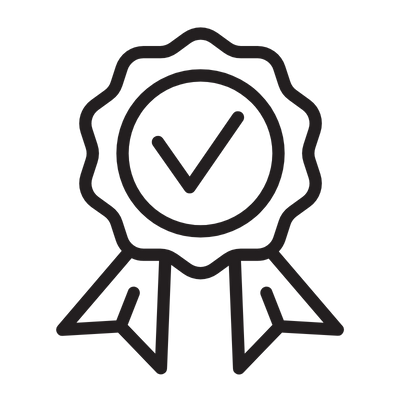
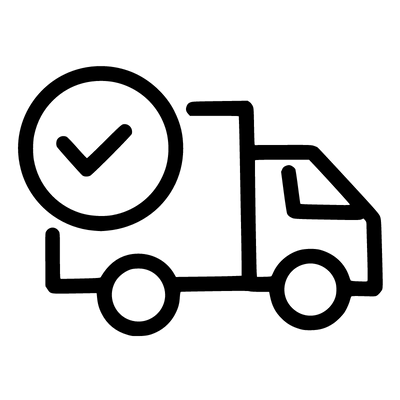
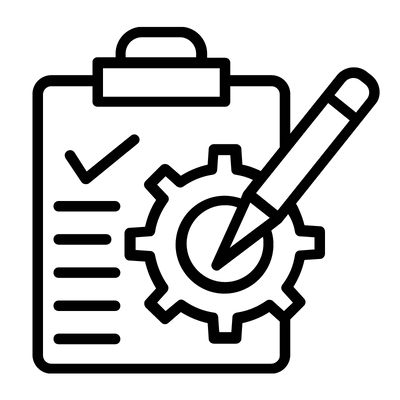
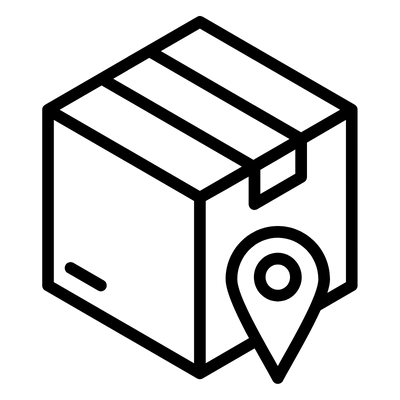
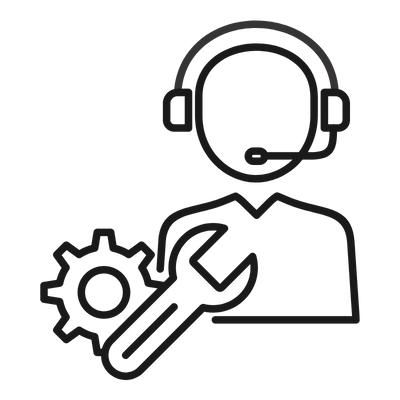
DTF Film Product Effect Display
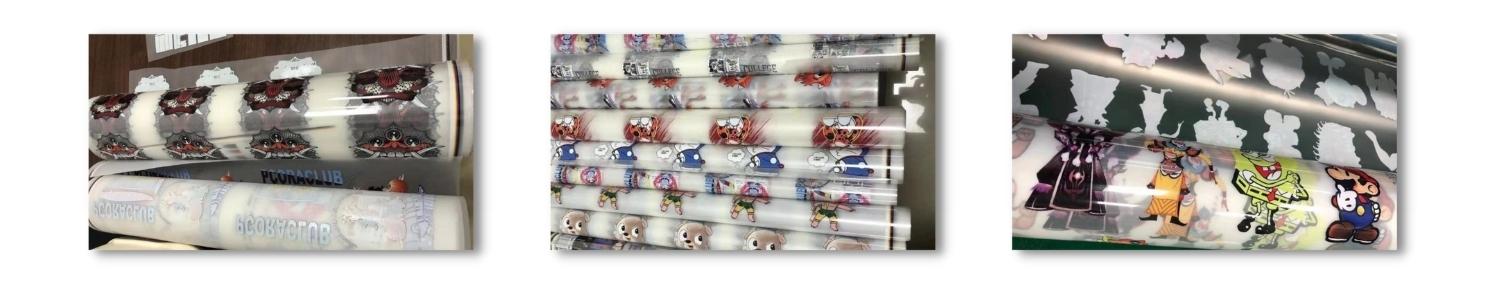
DTF Buying FAQ
DTF PET Film: Ultimate Guide to FAQs
Many people are asking, why choose DTF? Obviously this printing technique provides unique printing effects. Today we will popularize this printing technology and guide you to choose the correct printing method.
What is DTF
DTF printing is a flexible and latest printing technology on the market. It requires the use of a special film (DTF PET Film) on which you can print your design and use to transfer the image to the garment.
It's a short printing process where images are printed on clothes through a special film. With the help of heat and pressure, the image will stick to the garment permanently. DTF printing technology is versatile. It is suitable for a very wide variety of materials, including synthetic cotton fabrics, polyester and silk. Also, it is an economical printing method. On that front, the printer is affordable, and the process is short and very easy.
Advantage:
-
lifelike print
-
durable print
-
Support multi-color printing
-
Endless color options
-
Supports complete design personalization
-
Can handle small projects that require different print designs
-
Works with all garments
What is DTF printing?
Direct-to-Film (DTF) and sublimation printing are both thermal transfer technologies in the design printing industry. DTF is the latest printing service technology for decorating dark and light T-shirts on natural fibers such as cotton, silk, polyester, blends, leather and nylon without the need for expensive equipment. Sublimation printing uses a chemical process in which a solid immediately turns into a gas without passing through the liquid stage.
DTF printing is an upgraded alternative to DTG
Film transfers are printed using a specific kind of water-based ink. After the ink dries, apply the powdered glue to the back. Now it is heat cured and can be stored or used immediately. One of the benefits of DTF printers is that no preprocessing is required. After heat pressing, you can transfer the soft water-based ink to clothing within 15 seconds.
Durability of DTF Finished Products
DTF printing is ideal for workwear due to enhanced durability with special inks and adhesives. Due to the use of water-based inks, the print does not crack like screen printing because it feels very soft to the touch. This makes the system ideal for clothing such as workwear, high-end apparel, gym wear and cycling wear.
Quality equipment is essential
If you own a business that conducts digital printing business, then you must clear that the quality of your business is related to the quality of DTF printers and DTF inks. Purchasing quality DTF printers and DTF inks will give your business a vital boost.
Not all PET films are suitable
PET film is required for DTF printing, but this does not mean that every type of PET film is suitable for the DTF process. Poorer quality untreated films may be cheaper, but they simply can't match the performance of good quality films - they may stain, not accept adhesives, or ruin your clothes. The cold release film is specially treated to withstand the high temperature and pressure of heat presses; it is also compatible with all desktop and large format printers.
Fabrics do not require pretreatment with DTF technology
One of the many advantages of DTF printing is that garments do not require any pre-processing to accept transfer. This can simplify your operations and potentially reduce your costs. Overall, the DTF printing process is faster and requires less labor than DTG printing.
DTF printing offers greater versatility
When printing directly onto textiles, your options are limited. DTF gives you more flexibility as you can print on a variety of fabrics including cotton, polyester, rayon, nylon, silk, leather and more.
Similarities Between DTF and WTT
Both involve printing on film – a transparent PET-based material with a special coating suitable for a specific process. Both use white to provide the basis for CMY or CMYK colors. Both use "post-press" adhesive additives to provide durable adhesives to the substrate. Both thermal transfer applications support a wide range of cold peel substrate types and produce vibrant colors with fine detail and good durability.
Difference between DTF and WTT
First of all, their significant difference is the difference in printing time, which affects your production efficiency.
White Toner Transfer:
It takes about 15 seconds to print each transfer. Plus 75 seconds to transfer and 45 seconds to heat press the transfer to the garment.
You also usually need to trim the transfer a bit and take a few seconds to position it properly on the shirt.
So, if you're only doing one shirt, it's done in about 3 minutes or so.
Transfers can be printed and stacked right away, but if you're going to store them, it's best to combine them first.
DTF transfer:
About 2 minutes per shirt. The DTF printer uses a translucent DTF PET transfer film so when you heat press it onto the garment later you can see the design under the film. The thickness of the PET film is about 0.75mm for better transfer characteristics.
DTF printers use clear PET transfer film, when you heat press the film onto the garment, you can see the design under the film. This is a particular advantage and also saves some time.
The unique textile ink used in DTF improves upon traditional DTG inks by using smaller pigment sizes. Both DTG and DTF inks suffer from pigment settling issues that require vigorous agitation and frequent heavy cleaning cycles. However, while the larger pigments in DTG can cause clogging of the inkjet heads, this is not a problem for DTF inks. For WTT, these are not considerations.
DTF uses a slower inkjet printer to deposit a layer of liquid ink on film. After printing, while the DTF ink is still wet, apply the binder powder by shaking it on the paper and flicking the back of the paper to knock off excess powder. After the powder is applied, it needs to be melted and the ink dried. Everyone seems to have a different approach, from pancake pans to convection ovens and more. With that comes the risk of accidentally boiling the ink.
Why is DTF gaining popularity?
Direct-to-film (DTF) printing is a versatile technique that involves printing a design onto a special film for transfer to a garment. Its thermal transfer process offers similar durability to traditional screen printing. Many times people say that DTF is an upgrade from DTG, which is why it is growing so quickly.
DTF printing offers greater versatility than other printing technologies. DTF can print on a variety of fabrics including cotton, nylon, rayon, polyester, leather, silk and more.
DTF printing has revolutionized the textile industry and updated textile creation for the digital age. The process is simple: create digital artwork, print it on film, and transfer it to fabric.
How does DTF work?
DTF works by printing transfers on film, which are then heat pressed onto various garments. While DTG (direct to garment) technology is only available for cotton fabrics, many more materials are compatible with DTF printing.
DTF printers are affordable compared to DTG or screen printing technologies. DTF powder, printable double-sided cold peel PET film (for printing transfer films) and high quality DTF inks are required to get the best results.
DTF Printing Steps
Designing a DTF print is as easy as designing on paper: your design is sent from the computer to the DTF machine, and the printer does the rest. Although DTF printers look different from traditional paper printers, they function very similarly to other inkjet printers.
The simple DTF four-step process makes fabrics feel softer and provides better wash resistance.
Step 1: Insert the PET film into the printer tray and print.
Step 2: Apply hot melt powder to the printed image on the film.
Step 3: Melt the powder.
Step 4: Pre-press the fabric.
Features of DTF and DTG
-
DTG.
1. It requires pretreatment: For DTG, the process starts with pretreatment of the garment. This step is necessary before printing because we will be working directly on the fabric, which will keep the ink well and avoid transferring it to the fabric. In addition, we need to heat the garment before printing to activate this treatment.
2. Print directly on the garment: With DTG, you can print directly on the garment, so the process is shorter than DTF and no transfer is required.
3. Using white ink: We can choose to use a white mask as a substrate to ensure that the ink does not mix with the color of the medium, although this is not always necessary (for example on white substrates) and it is also possible to place white only in certain areas to reduce the use of this mask.
4. Cotton print: This print can only be printed on cotton garments.
5. Final Press: To fix the ink, we must perform the final press at the end of the process, where we will prepare the garment.
-
DTF
1. No pre-treatment: In DTF printing, the fabric does not need pre-treatment because it is pre-printed on the film and must be transferred.
2. Print on film: In DTF, we print on film and then the design must be transferred to the fabric. This can make the process a little longer compared to DTG.
3. Gum Powder: This type of printing requires the use of gum powder, which is applied immediately after the ink is printed on the film. On printers created for DTF, this step is included in the printer itself, so you can avoid any manual steps.
4. Use white ink: In this case, a layer of white ink is required, placed on top of the colored layer. This is a color that is transferred to the fabric and used as the base for the main color of the design.
5. Any type of fabric: One of the advantages of DTF is that it allows you to use any type of fabric, not just cotton.
6. Transfer from film to fabric: The final step of the process is to remove the printed film and transfer it to the fabric using a press.
More advantages of DTF printing
In contrast, screen printing involves dozens of steps, which means it's usually only cost-effective for the simplest designs or for printing large quantities of items.
While screen printing still has a place in the apparel industry, DTF printing is more affordable for small businesses or textile organizations that want to make smaller orders.
DTF printing offers more design options
Screen printing complex patterns is not feasible due to the amount of work involved. However, using DTF technology, printing complex, multi-color graphics is different from printing simple designs.
DTF also allows creators to create DIY hats, handbags and other items.
DTF printing is more sustainable and less costly than other methods
With the fashion industry's growing interest in sustainability, another advantage of DTF printing over traditional printing is its highly sustainable technology.
DTF printing helps prevent overproduction, which is a common problem in the textile industry. In addition, the inks used in digital direct-jet printers are water-based and environmentally friendly.
DTF printing allows for one-off designs and eliminates waste of unsold inventory.
Compared to screen printing, DTF printing is less expensive. For small orders, DTF printing has a lower printing cost per unit than traditional screen printing processes.
What is the difference between DTF and Sublimation printing
DTF printing involves the transfer of an image onto a fabric or material using DTF PET film. In contrast, sublimation printing uses sublimation paper. What are the differences and advantages and disadvantages of these two printing techniques?
-
DTF Advantages.
1. DTF printing can be done on almost all types of fabrics
2. In contrast to DTG, no pre-treatment is required
3. The fabric has good washing characteristics.
4. DTF process is less cumbersome and faster than DTG printing
-
DTF Disadvantages.
1. slightly different feel in the print area compared to thermal sublimation printing
2. Color vibrancy is slightly lower than sublimation printing.
-
Sublimation Advantages.
1. can be printed on rigid surfaces (cups, photo slabs, plates, clocks, etc.)
2. Very simple and very easy to learn
3. it has an unlimited range of colors. For example, thousands of different color combinations are possible with four-color inks (CMYK).
4. There is no minimum print run.
5. Orders can be produced the same day.
-
Sublimation Disadvantages.
1. The fabric must be made of 100% polyester, or at least use about 2/3 polyester.
2. Only special polyester coating can be used for non-woven substrates.
3. The item must have white or light-colored printed areas. Sublimation does not work well on black or dark colored fabrics.
4. If permanently exposed to direct sunlight, the color can fade within a few months due to the effects of UV light.
At wellye, we sell both DTF film and sublimation paper and ink. They are of the highest quality and use the latest technology to achieve bright and vivid colors on your fabrics.
In general, DTF transfers achieve photo-quality images and are superior to sublimation. The higher the polyester content of the fabric, the better and more vibrant the image quality. For DTF, the design on the fabric is soft to the touch. You will not feel the sublimated design when the ink is transferred to the fabric. DTF and sublimation use different heating temperatures and times for transfer.
How you should decide to use DTF and DTG
So, what factors should we consider when deciding which print to choose?
Our printing material: As mentioned above, DTG can only be printed on cotton, while DTF can be printed on many other materials.
Production volume: Currently, DTG machines are more versatile than DTF, allowing for larger and faster production. Therefore, it is important to be clear about the production needs of each company.
Results: The end result of one printout is very different from another. In DTG, the drawing and ink blend into the fabric and feel rougher, like the base itself, while in DTF, the solid color powder makes it feel plastic, brighter and less blended into the fabric. However, this also gives the impression of higher color quality because they are solid colors and do not interfere with the base color.
Use of white: A priori, both technologies require a considerable amount of white ink to print, but using good software, you can control the white layer applied in DTG according to the base color, thus reducing the cost significantly.
What is direct inkjet printing?
Inkjet printing is a type of computer printing that recreates digital images by ejecting droplets of ink onto paper and plastic substrates. Inkjet printing is a popular choice for printing needs. Images are created by precisely ejecting thousands of tiny ink droplets onto paper, similar to how TV and computer screens render images through clusters of thousands of pixels.
What is the difference between DTF ink and direct inkjet printing ink
-
Different craftsmanship
The application of DTF (offset heat transfer) is to print the ink on the thermal transfer film, then sprinkle a layer of hot melt powder on the surface of the thermal transfer film, and then develop the color by pressing; while the application of direct inkjet coating ink is direct Printed on fabric, the fabric is in the printing process.
In order to achieve better color and color fastness, it is often necessary to use pre-treatment liquid and post-treatment liquid together. The process is more complicated than the DTF heat transfer process, and more professional customers are often required to complete the entire direct coating process. The DTF (offset heat transfer) process is relatively simple, and it is easy for customers to quickly grasp the process and copy and promote it.
-
Different feel
Direct inkjet feels better than DTF offset heat transfer. In DTF offset thermal transfer applications, there is a layer of hot melt powder between the ink and the fabric. The hot melt powder is transferred to the fabric as a binder along with the ink. The ink of direct spray coating is directly printed on the fabric, so there is generally no problem of hand feeling. In terms of feel, direct spraying of paint has obvious advantages. On the other hand, with the maturity of the application of DTF offset heat transfer process, the application performance of hot melt powder has been improved, and the finished product made by DTF offset heat transfer application can also meet the needs of market customers.
-
Different color expressiveness and fastness
DTF heat transfer excels in color expression and fastness. In order to improve the color and fastness of coating direct spray application, it is often necessary to cooperate with pre-treatment and post-treatment liquids to achieve better results, and the use of hot melt powder in DTF offset heat transfer applications perfectly solves the problem of color and fastness. Using hot-melt powder as a binder, the DTF ink is perfectly combined with the fabric, and the color expression and fastness performance after color development are very good. The color fastness problem is a very headache in the application of direct-injection coatings. By using hot melt powder as an intermediate medium, DTF ink and fabric can be well matched, which perfectly solves the long-standing color fastness problem in direct-injection printing applications.
-
Plans vary in cost
In terms of ink prices, DTF offset thermal transfer inks are cheaper than direct-to-paint application inks. The cost of DTF offset thermal transfer applications is thermal transfer film, and the price of thermal transfer film is also falling. Overall, DTF offset thermal transfer applications cost less than direct inkjet applications. DTF heat transfer application scheme has low investment threshold, simple process, easy entry and replication,
Many people are asking, which is better, DTF or Screen print transfer, which should I choose? Clearly these two printing techniques provide unique printing effects. Today we will compare the two printing technologies and guide you in choosing the right printing method.
What is Screen Printing
Screen printing is a printing process that requires the use of a squeegee, thick ink and screen to transfer a stencil design, usually onto some paper or fabric. With some special inks, the technique can be used on glass, plastic, metal and wood.
With this technique, plastisol-based inks are pressed through a screen onto clothing, such as polo shirts, sweatshirts, baseball caps, or other items. Different screens are used for different colors. The screen is attached to a printing press, which rotates and allows the design to be printed on the garment. Although screen printing is an analog process, when you place an order for printing, you typically send your design files in formats like EPS to the printing company.
The basis of this technique is to make a stencil design on a mesh screen. Once you've set it up on a product, say a piece of clothing, you can put ink on it. After that, push it through the grid to print on the material below.
Screen printing requires a certain set-up as only one color can be applied at a time.
Advantage:
-
The best way to mass-produce t-shirts on a budget.
-
Master screen printers can produce amazing results.
Shortcoming:
-
Not a one-time order. It takes a long time to set everything up for each design. However, once everything is in order, you can quickly print a large number of shirts.
-
Screen printing is an art form. It has a steep learning curve and requires a lot of practice to do well.
-
More space is required for production.
-
It is a messy printing method involving spraying, water washing, ink mixing, chemicals, etc.
DTF vs Screen Pring Transfer
DTF printing and screen printing are similar in many ways. Products produced by both techniques are durable, can withstand multiple washes and still have good color performance. But their differences determine how you ultimately choose to conduct your production and business to meet your needs and operations.
-
Printing Technology
Screen printing requires the use of stencil designs to transfer your designs. On the other hand, DTF printing requires PET DTF Film to transfer your design.
The DTF printing process involves the use of a DTF printer, whereas screen printing uses stencil design.
-
Print Quality
From vivid design to finish, DTF printing has the best print quality. This is something that screen printing does not have.
But even so, the screen-printed print quality is commendable and fairly durable.
DTF works best on a variety of fabrics, but is surprisingly detailed when dealing with multicolor prints.
-
Color Options
DTF has a variety of color options for printing. It allows you to print graphic designs in any number of colors, each with guaranteed lifelike quality. Screen printing, on the other hand, limits you to a few color options. To make matters worse, dealing with complex color mixing is challenging.
So relatively speaking, DTF is more suitable for producing your unique design.
-
Cost-effectiveness
Both designs are cost effective. However, screen printing is less cost effective in some cases. For example, when you're working on large projects that require the same type of printing, screen printing is fine. In this case, this is the cheapest method. However, if you're dealing with different designs, the cost will be higher because of the high cost of setting up each print screen.
On the other hand, DTF printing is reliable whether you're working on large or small projects. Screen printing is flexible and inexpensive when dealing with bulk orders that require different print designs.
-
Production Quantity
When it comes to the number of prints, there are significant differences between the two processes. While both technologies can handle large orders, they differ in efficiency. For example, screen printing requires creating a screen for each design. Therefore, it may take longer to complete multi-color printing.
But with DTF, you can enjoy an efficient printing process even for bulk orders. However, if you are doing the same type of printing on multiple products, then screen printing can work well. It can process the same type of printing on bulk orders efficiently and quickly.
Therefore, you need to specifically consider your production needs when choosing a production method.
What is the better type of print for you
As mentioned earlier, with DTF, you don't need to worry about making screens, separating artwork by color, or worrying about the number of colors that will affect the cost and difficulty of printing. While screen printing may be the cheapest way to mass-produce t-shirts, you may still run into limitations with artwork and clothing. You need to be a screen printing master to consistently achieve high-quality results.
Screen printing also requires considerable space and space for the various steps in the process. Many early adopters of DTF were screen printers who wanted to keep high-color, complex jobs on their screen printers.
In short, if you're looking for a printer that can deliver bulk items, choose DTF printing. It's fast, efficient, and has very few processes to complete. However, if you need high-quality printing that doesn't require customization, then screen printing is fine.
Reasons to choose DTF
-
DTF printing is ideal for small and medium businesses
The DTF process enables creators to get started faster than silkscreen technology.
In contrast, screen printing has a relatively long learning cycle and initial cost.
Designing a DTF print pattern is as easy as designing on paper: your design is sent from your computer to the DTF machine, and the printer does the rest. While DTF printers look different from traditional paper printers, they function very similarly to other inkjet printers.
By contrast, screen printing involves dozens of steps, which means it's usually only cost-effective for the simplest designs or printing large numbers of items.
While screen printing still has its place in the apparel industry, DTF printing is more affordable for small businesses or textile establishments that want to place small orders.
-
DTF printing offers more design options
Screen printing complex patterns is not feasible due to the amount of work involved. However, with DTF technology, printing complex multi-color graphics is different from printing simple designs.
-
DTF printing is more sustainable and less expensive than other methods
With the growing interest in sustainability in the fashion industry, another advantage of DTF printing over conventional printing is its highly sustainable technology.
DTF printing helps prevent overproduction, a common problem in the textile industry. Also, the inks used in digital direct inkjet printers are water-based and environmentally friendly.
-
DTF printing enables one-off designs without wasting unsold inventory.
Compared to screen printing, the initial cost of DTF printing is lower. For small batch orders, the unit printing cost of DTF printing is lower than the traditional screen printing process.
Benefits of using DTF Film
-
Suitable for a wide range of materials
While direct-to-garment printing works best on 100% cotton, DTF is suitable for many different garment materials: cotton, nylon, treated leather, polyester, 50/50 blends, and light and dark fabrics. Transfers can even be applied to different types of surfaces, such as luggage, shoes, and even glass, wood and metal! You can expand your inventory by using DTF to apply your designs to a variety of items.
-
No pre-processing required
If you already have a DTG printer, you are probably familiar with the pre-processing process (not to mention the drying time). The hot-melt capability applied to the DTF bonds the print directly to the material, which means no pre-processing is required!
-
Use less white ink
DTF requires less white ink - about 40% white, while DTG printing requires 200% white. White ink tends to be the most expensive because it is used more, so reducing the amount of white ink used for printing can save a lot of money.
More durable than DTG printing
DTG prints undeniably have a soft, almost hand-free feel because the ink is applied directly to the garment. While DTF prints do not have the soft feel that DTG boasts, transfers are more durable. Direct transfers to film wash well and are flexible - which means they won't crack or peel, perfect for heavy use items.
-
Easy to design
DTF transfers on means you can place designs on hard-to-reach or awkward surfaces. If the area can be heated, you can apply a DTF design to it! Because only heat is needed to adhere the design, you can even sell your print transfer directly to your customers and allow them to ease the design onto any surface or item they choose without the need for special equipment!
-
Faster Production Process
Because you can eliminate the steps of pre-treating and drying garments, you can significantly reduce production time. This is great news for one-off or small batch orders that are traditionally unprofitable.
-
Help make your inventory more diverse
While it may not be feasible to print a large number of the most popular designs on every size or color of garment, with DTF printing, you can print popular designs ahead of time and use very little space for storage. Then, you can always have your best sellers ready to apply to any garment as needed!
Disadvantages of DTF printing
-
Full-size printing is not as good as direct-to-garment (DTG) printing.
-
Different hand feel compared to direct-to-garment (DTG) printing.
-
Safety equipment (protective glasses, face shield and gloves) must be worn when using DTF products.
-
DTF adhesive powder must be kept in a dry environment. High humidity can cause quality problems.
How do I use DTF Film for transferring?
Step 1: Print on the Film
Insert the PET Film into the printer tray.
Click Print.
The inkjet printer will "Print directly to Film", transferring the image to your PET Film.
When removing the print from the tray, be careful not to smudge the print!
Step 2: Apply the powder
This step is to apply DTF powder to the film on which the image is printed.
You must apply the powder while the print is still wet!
Make sure to apply the powder evenly.
Typically, you would place a tray next to the printer, sprinkle the powder on the roll of paper, and swing it back and forth until it covers the wet ink. Then carefully shake off the excess.
Or, you can use an automatic shaker available for busy custom t-shirt stores.
Step 3: Melt the powder
As the description indicates, your next step is to actually melt the powder into place.
The most common method is to place the direct transfer DTF transfer film into the oven for about 2 minutes.
Or, if you are already in the business of making custom t-shirts with DTG or vinyl or white toner printer transfers, you can use a heat press. Just make sure you hover without applying any pressure. Or the top of the media is not in contact with the transfer at all.
There is no intentional curing time and temperature for DTF transfers. Better check with the DTF film manufacturer!
Step 4: Pre-press the material
Of course, it does not have to be a T-shirt. However, whether you are applying a DTF transfer, a sublimation transfer, or any other transfer method, it should be completely smooth. Any wrinkles will appear on the print!
Perhaps more importantly, it will completely dry the material. You'd be surprised how much moisture the fabric can absorb from the moisture in the air, which can affect print quality.
Step 5: Apply DTF Transfer
The PET film with the image and molten powder is placed on the pre-pressed material in the heat press. You will then heat press the transfer material onto the shirt as you would anything else, following the current manufacturer's instructions.
Unlike throwing a screen printed shirt into a tunnel dryer, this process is usually recommended to take less than 30 minutes.
Step 6: Peel DTF Transfers
Most DTF Films can be cold peeled, but hot peeled films are also available.
Therefore, after hot pressing onto the shirt, set it aside until the fabric and transfer material have cooled completely.
If you are making a series of shirts, you can press them down one after the other, glassing them depending on the type of DTF Film used. The cooled hot melt acts as a binder, binding the colored pigments in the ink to the fibers of the fabric.
1.Suitable for a variety of materials
While direct garment printing works best on 100% cotton, DTF is suitable for many different garment materials: cotton, nylon, treated leather, polyester, 50/50 blends, and light and dark fabrics. Transfer can even be applied on different types of surfaces such as luggage, shoes and even glass, wood and metal. You can expand your inventory by using DTF to apply your designs to a variety of projects.
2.No preprocessing required
If you already own a DTG printer, you're probably very familiar with the preprocessing process (not to mention drying times). The hot melt capability applied to DTF transfer bonds the print directly to the material, which means no pretreatment is required.
3.Save white ink
DTF requires less white ink - about 40% white, while DTG printing requires 200% white. White ink is often the most expensive, because it is used more, and the pigment is titanium dioxide, so reducing the amount of white ink used for printing can save a lot of money.
4.More durable than DTG printing
There is no denying that DTG prints have a soft, almost tactile feel as the ink is applied directly to the garment. While DTF printing does not have the soft feel that DTG has, the transfer is more durable. Transfer directly to film washes and are flexible - meaning they won't crack or peel, making them ideal for frequently used items.
5.Color
DTF excels in color expression and fastness. In order to improve the color and fastness of coating direct spray application, it is often necessary to cooperate with pre-treatment and post-treatment liquids to achieve better results, and the use of hot melt powder in DTF offset heat transfer applications perfectly solves the problem of color and fastness. DTF hot-melt powder is used as a binder, so that the DTF ink and the fabric are perfectly combined, and the color expression and fastness performance after color development are very good. The color fastness problem is a very headache in the application of direct-injection coatings. By using hot melt powder as an intermediate medium, DTF ink and fabric can be well matched, which perfectly solves the long-standing color fastness problem in direct-injection printing applications.
6.Easy to use
The application of DTF is to print the ink on the thermal transfer film, then sprinkle a layer of hot melt powder on the surface of the thermal transfer film, and then develop the color by pressing; while the application of direct inkjet coating ink is directly printed on the fabric, The fabric is in the printing process, in order to achieve better color and color fastness, it is often necessary to use pre-treatment liquid and post-treatment liquid together. The process is more complicated than the DTF heat transfer process, and more professional customers are often required to complete the entire direct coating process. The DTF (offset heat transfer) process is relatively simple, and it is easy for customers to quickly grasp the process and copy and promote it.
7.Faster production process
Since you can eliminate the steps of pre-processing and drying garments, you can significantly reduce production time. That's good news for traditionally unprofitable one-off or low-volume orders.